Quality
There is no alternative to quality. Because giving the best is to value the customer.
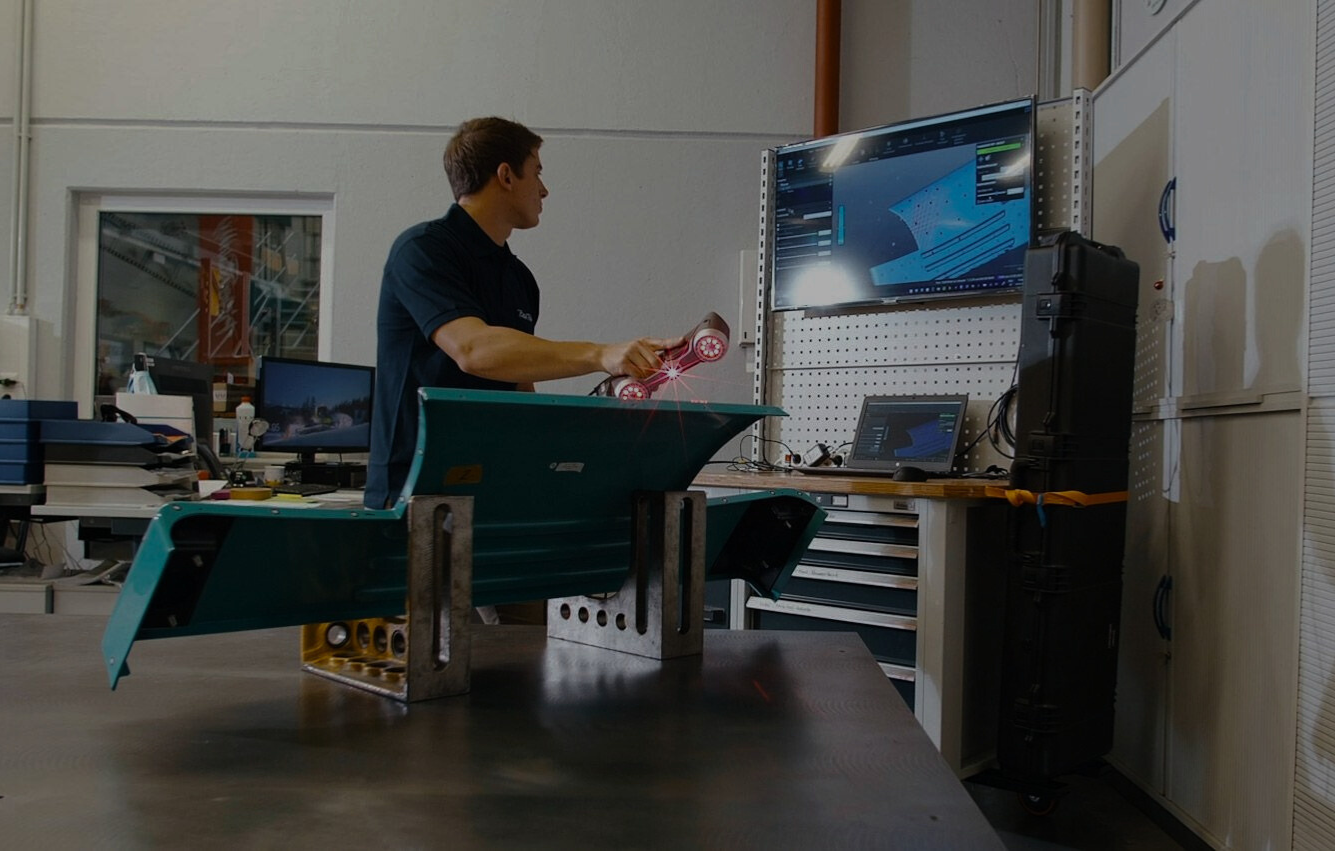
Quality to the highest standard
Each and every component is tested for reliability and functionality as part of extensive test programmes. Tests down to -40 degrees are run in the cold chamber to see if the engines would start in the most adverse weather conditions and whether the entire drive train would work perfectly at any temperature. In parallel with these endurance tests, supplier quality as well comes in for close scrutiny. Suppliers do not merely undergo a rigorous selection process but the parts they supply are subject to an ongoing checking process as well. On three levels.
The Kässbohrer Geländefahrzeug AG quality assurance people are involved right from the production of the models and tooling. Then there is a thorough quality inspection of the first pre-production samples and finally the Laupheim specialists gain a thorough understanding of how the parts are manufactured in series conditions.
We perform vehicle audits in addition to the routine end checks at PistenBully and subsequent release by our quality centre. We perform further function testing with attachments on individual vehicles randomly selected from the delivery-ready stock. This is how we simulate transfer of the vehicle to the customer.
To guarantee lasting continual improvement, the Kässbohrer Geländefahrzeug AG has implemented comprehensive quality management in all business processes and is certified in accordance with the internationally recognised quality management standard ISO 9001:2015 The process security achieved in this way in many areas, actually leads to better quality products.
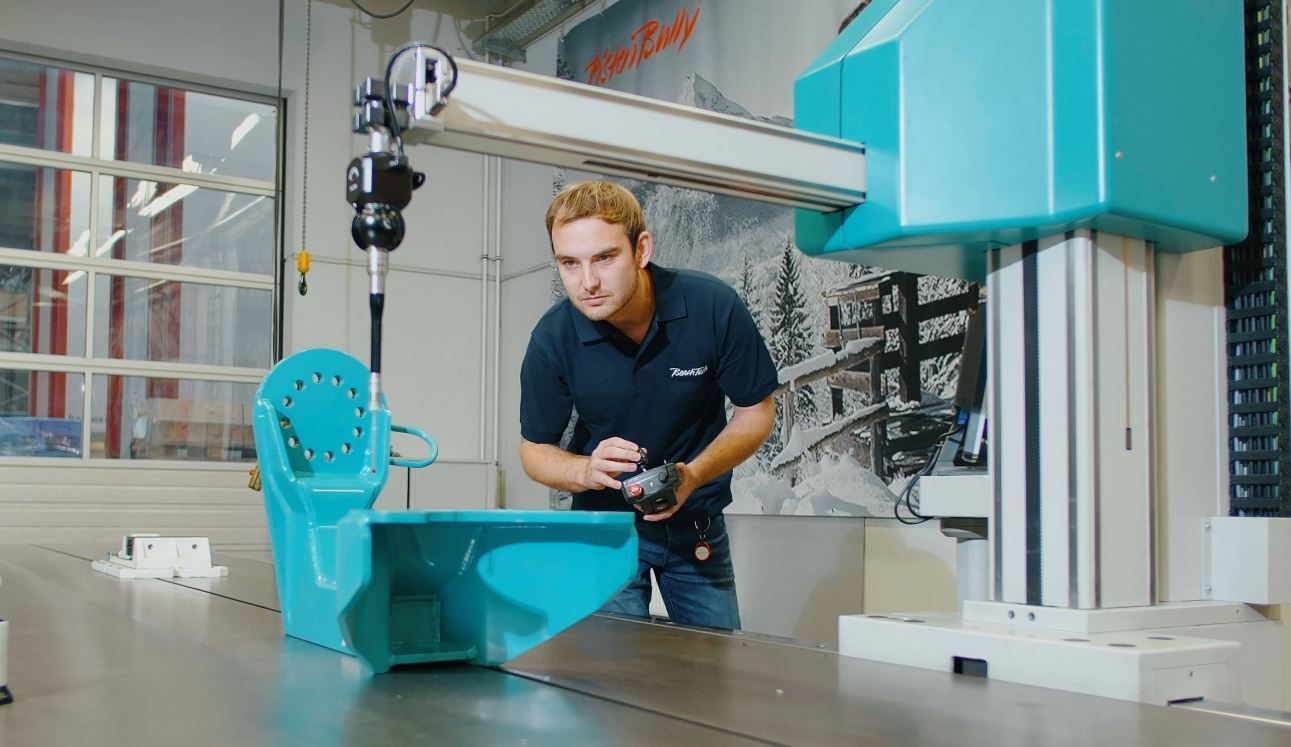
“Quality processes before, during and after production have top priority.
Kässbohrer quality promise
The Kässbohrer quality promise consists of different building blocks.
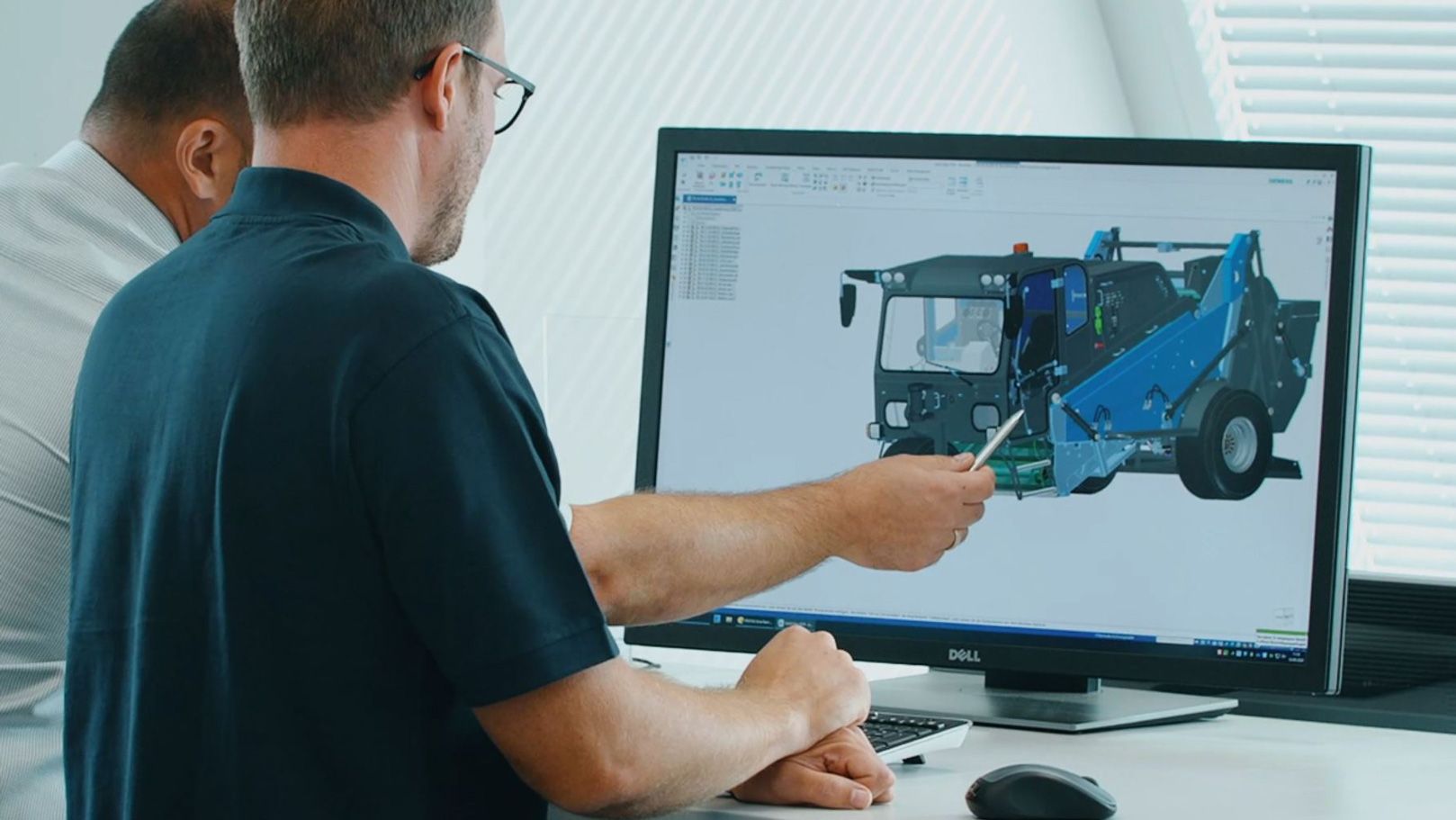
Kässbohrer invests a lot of time in the development of vehicle components and also involves its customers and suppliers in the process. Kässbohrer's quality assurance department conducts audits at suppliers' facilities before and during component production to ensure workflows, production processes and component quality.
When the components are delivered, the incoming goods inspection goes into action. The inspection is carried out using the latest measuring technology. Kässbohrer places the highest demands on material quality and fitting accuracy in order to meet the customers' quality requirements.
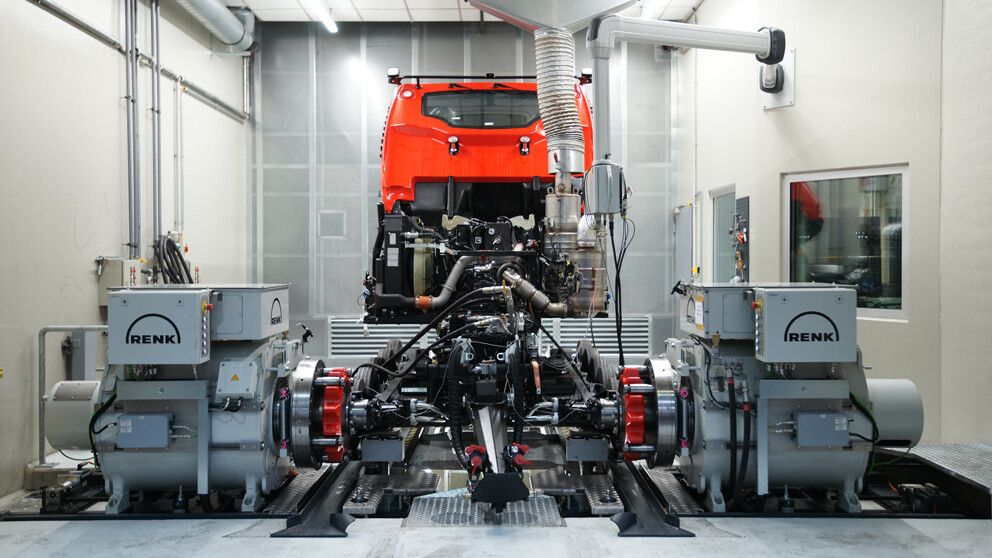
Each vehicle is marked with a barcode that is scanned. This gives the vehicle its individual test program. The digitized and automated processes eliminate the often time-consuming set-up times required for changing over to the vehicle to be tested. The test sequences are transparent and reveal all details about the vehicle. As a result, testing is not only fast and efficient, but above all flexible, as we can produce smaller batches of a model more easily - depending on demand.
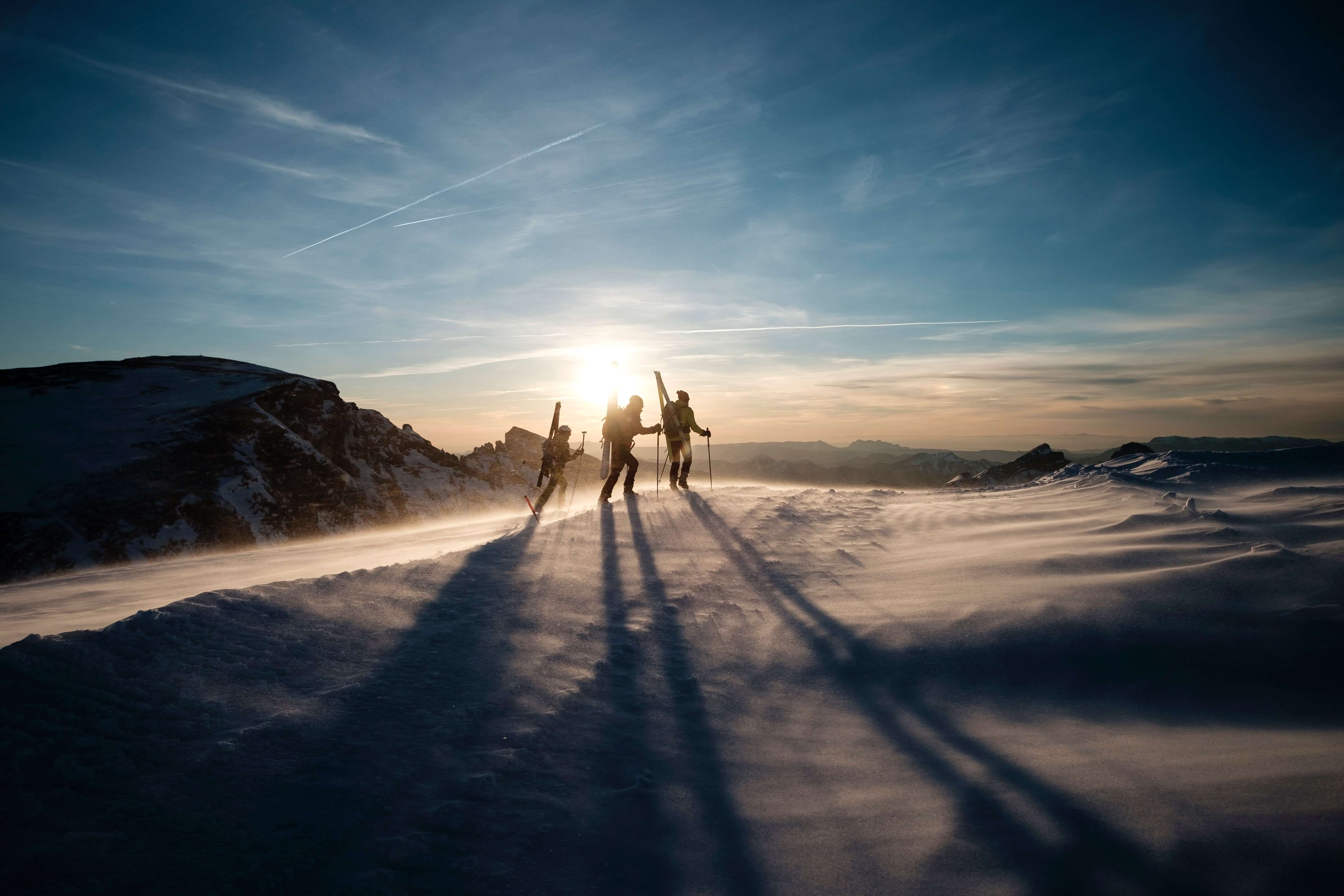
During the development of a new vehicle, service and design work closely together in a continuous improvement process to ensure the best possible quality and guarantee that customer wishes and requirements are met. The service team accompanies the delivery and puts several vehicles, at randomly selected customers, through their paces again after about 100 hours of operation. Findings are reported directly back to production.